The Pursuit of QA Excellence
Maintaining a specific service standard is a goal every pest management company strives for regardless of the size or complexity of the account. But it is often one of the most vexing tasks pest control companies face.
How did Sprague Pest Solutions take on the challenge? They formed an independent, in-house quality assurance (QA) team to achieve consistently high service levels. Unlike other pest control companies, Sprague’s QA team is separated from the service center and dispersed across the company’s 10-state service footprint. And the one auditor for every 50 route-manager ratio allows for greater attention to detail.
Sprague’s QA team features professionals with decades of experience and deep knowledge in both pest control and third-party audit practices. The team is a reinforcement of the company’s long held commitment to using science backed, integrated pest management (IPM) pest control practices and delivering uncompromising service to their customers.
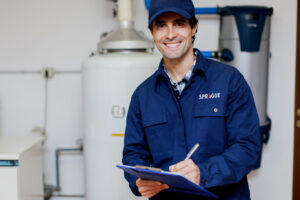
With the QA team in place Sprague’s route managers are not reacting to an auditor’s report but rather are proactive, with adjustments made before the audit.
“Your company’s culture is often defined on where you put your resources,” says AJ Treleven, ACE, director of operations for Sprague. “If you claim to be built on quality, it is hard to make that claim if you can’t back it up and don’t invest. The investment in our QA team allows us to walk the talk when it comes to quality.”
Treleven says QA team members do not operate in a silo or vacuum, and that their sole job is to measure and calibrate how effective Sprague’s service is and identify clients’ needs.
Finding Solutions
Sprague has built its reputation on long-term client relationships, and that can only be achieved by standing behind their service quality. Reaching that standard starts with tapping into the QA team’s experience and building trust with clients.
With the QA team in place Sprague’s route managers are not reacting to an auditor’s report but rather are proactive, with adjustments made before the audit. This helps deliver a higher quality service, reduces stress for clients and builds confidence in their pest control programs. And as shifts occur with third-party audit standards and client requirements, especially organic food processing facilities, the Sprague QA team can pivot and adapt.
Martha Branch, one of four Sprague QA auditors, says the QA team looks for ways to improve clients’ pest programs every day.
“We pride ourselves that our internal audits should be the toughest ones a client has to deal with,” says Branch. “Our mission is to protect the client and look out for their best interests when it comes to pest control and food safety. We expect them to receive a perfect audit score.”
The Sprague QA team audits are done with no advance notice, and all areas of the client’s pest control program are reviewed. They seek to identify conditions that could promote, or result in, a pest issue and work with the Sprague route manager and the client to ensure adjustments and corrective actions are taken and documented.
The team makes sure that not even the smallest detail falls through the cracks, and Branch says clients appreciate the investment Sprague is making in their business.
An example of where Sprague’s QA team dug deeper to identify the source of a pest issue took place in a cheese packaging facility that Branch was inspecting. The facility was experiencing an Indian meal moth problem; an unusual pest for cheese production, given that the pest is usually found in facilities that are processing grain, nut, or cocoa-based foods, not cheese.
After a thorough inspection of the facility’s storage areas and transportation coolers, there was no sign of the source of the infestation. As she continued her inspection she noticed a large tarp – roughly 20’ x 20’ – in the middle of a storage room covering something.
Thinking it was a food commodity or ingredient Branch lifted the tarp only to discover a stack of wooden beehives. The hives were being stored there by the owner and the honey residue inside the hives was attracting the moths. The hives were removed, and the pest infestation was resolved.
Results
Finding the source of the Indian meal moth problem in the cheese packaging facility is just one example of the significant value the Sprague QA team delivers for clients.
During an inspection of a food distribution warehouse, a Sprague QA auditor noticed the client started storing chocolate in a room that was not previously used for commodity storage. The client operated multiple facilities that were serviced by Sprague and the auditor, having inspected the client’s other facilities, knew the client had done something similar at another location, and an Indian meal moth issue ensued.
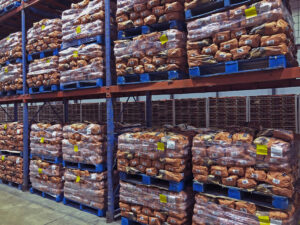
Sprague QA audits provide protection for customers who receive third-party audits or inspections..
The auditor took the proactive approach of having the route manager install pheromone monitoring traps in the room (they were not previously installed since no commodities were stored there). No pests were observed in the traps and the client had peace of mind they were protected.
The ultimate compliment for a service company is when your work proves its worth. Branch recalls a client – a large wet processing food manufacturer with multiple locations and brands, that Sprague took over service for from another company. The client was originally resistant to the QA audit process, but after Sprague performed its first audit the client was impressed with the level of detail and the value the checks and balances the audit delivered.
Why QA Audits Matter
- Provides protection for customers who receive third-party audits or inspections.
- Creates opportunities for collaboration between clients and their pest control service provider.
- Establishes a proactive approach to preventing pest issues.
- Increases quality, builds trust, and confidence in the services provided by focusing on a culture of continuous improvement.
The Sprague Solution
For more information on how Sprague Pest Solutions Quality Assurance and pest management services can protect your brand and keep your facility pest-free, visit our website or call 800.272.4988.